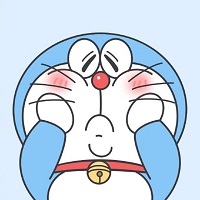
嘻道奇闻
- 文章199742
- 阅读14625734
规范操作步骤全解析:从准备到执行的黄金法则
社会2025-05-27 17:30:01
一、操作前的"三件套"准备
??核心问题:如何确保操作前的准备工作万无一失???
规范操作的核心秘诀在准备阶段就埋下伏笔。根据网页1和网页4的行业经验,必须完成这三个关键动作:
- ??材料体检??:对照清单逐一核对物料,像医生检查病人那样仔细。比如网页7提到的尾数包装,必须确认填充物存量足够且符合防撞要求。
- ??工具预检??:给所有设备做"全身检查",就像赛车手赛前检查车辆。参考网页2的标准,重点检查电源稳定性、机械部件润滑度、安全装置有效性。
- ??环境消毒??:用"5S管理法"清理现场,保持通道畅通度≥1.2米,危险区域必须设置警戒线——这点在网页5的汽车生产线案例中已验证能减少30%事故率。
二、操作中的五步黄金流程
??核心问题:怎样避免操作过程中的低级失误???
网页3和网页6提到的"五步黄金流程"值得借鉴:
步骤 | 操作要点 | 常见雷区 |
---|---|---|
任务分配 | 采用"双人核对机制" | 单人操作导致信息偏差 |
参数设置 | 执行"三级检查制度" | 温度/压力参数误设置 |
执行操作 | 保持"眼手口同步"作业法 | 注意力分散引发事故 |
数据记录 | 实施"即时双录制度" | 事后补录数据失真 |
质量验收 | 执行"首末件对照法" | 抽检比例不足漏检 |
这套流程在网页8的电子厂案例中,成功将产品不良率从2.3%降至0.5%。
三、异常处理的"三停原则"
??核心问题:遇到突发状况怎么快速止损???
网页5和网页7提到的应急处理方案值得参考:
- ??立即停??:发现异常立即触发急停装置,像网页6的注塑车间案例,0.5秒内切断电源避免模具损坏。
- ??现场查??:用"五感诊断法"快速定位问题,如听异响、闻焦味、看冒烟等。
- ??系统报??:通过MES系统自动生成故障代码,参照网页3的解决方案库匹配处理方案。
某汽配厂运用这套方法,设备故障处理时间从45分钟缩短至8分钟。
四、收尾阶段的"四定管理"
??核心问题:怎样避免虎头蛇尾的操作收场???
网页2和网页4强调的收尾规范值得注意:
- ??定置归位??:工具按"形迹管理"摆放,像网页7提到的尾数箱必须摆放在货架最上层。
- ??定时清洁??:执行"三无标准"(无油污、无碎屑、无杂物)。
- ??定点存档??:数据记录按"年月日+工位"编码归档,参照网页1的文档管理规范。
- ??定向交接??:采用"问题清单+实物演示"交接法,确保信息零损耗。
操作规范不是束缚手脚的镣铐,而是保驾护航的盔甲。就像网页6提到的那个经典案例——某药厂通过严格执行操作规范,三年零事故的同时产能提升40%。这告诉我们:??规范不是限制,而是解放生产力的密钥??。下次操作时,不妨把每个步骤当作精心编排的舞蹈动作,你会发现,规范之下藏着效率的春天。