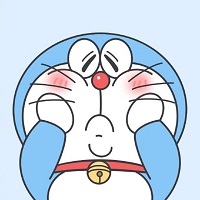
嘻道奇闻
- 文章199742
- 阅读14625734
丙烷裂解制乙烯技术解析收率提升与经济性突破
基础问题:丙烷裂解制乙烯的核心原理与挑战
丙烷裂解制乙烯是通过高温蒸汽裂解反应将丙烷分子(C3H8)分解为乙烯(C2H4)、丙烯(C3H6)等低碳烯烃的过程。其核心反应机理包括碳链断裂和自由基重组,反应温度通常控制在750-920℃,并需添加稀释蒸汽以降低烃分压、抑制结焦。丙烷单独裂解时乙烯收率约39%,若与石脑油共裂解,双烯总收率可达56%,但乙烯收率会降低5个百分点。
该技术的主要挑战在于:①高温条件下炉管结焦导致运行周期缩短(约需每40天清焦一次);②原料转化效率受分子结构影响,丙烷裂解需比乙烷裂解更高的能耗;③经济性对原料价格波动敏感,需平衡丙烷采购成本与乙烯市场价差。
场景问题:如何优化工艺参数提升收率
-
??裂解温度与停留时间的精准调控??
丙烷裂解温度每升高10℃,乙烯收率可提升1.5-2%。实验数据显示,在890-920℃区间内,乙烯收率从36%增至41.5%,但丙烯收率下降4%,需通过缩短停留时间(如采用毫秒裂解技术)减少二次反应。例如东方化工厂将共裂解温度控制在843-845℃,使乙烯单耗降低12%。 -
??稀释蒸汽比的动态调整??
降低稀释蒸汽比例(从0.5降至0.3)可提高炉管处理能力20%,同时减少能耗15%。但需平衡结焦风险,采用分段蒸汽注入技术可维持裂解选择性。 -
??原料混合裂解的协同效应??
丙烷与石脑油共裂解时,双烯总收率提升8-10%。镇海炼化通过混合进料(丙烷占比30%)使装置综合效益提高18%。此外,掺炼加氢尾油等重质原料可降低原料成本,但需配套急冷锅炉优化热量回收。
解决方案:经济性突破的关键路径
-
??催化剂与反应器创新??
开发CrOx/Ti-Al2O3等非贵金属催化剂,在650℃低温条件下实现丙烷脱氢制丙烯联产乙烯,选择性提升至85%。采用下行式反应器可缩短停留时间至0.1秒,乙烯收率突破42%。 -
??设备升级与热能回收??
万华化学引入SRT-VI型裂解炉,热效率从92%提升至95%,燃料消耗降低8%。急冷锅炉余热发电系统可回收30%热能,单吨乙烯能耗降至25GJ。 -
??产业链一体化布局??
PDH(丙烷脱氢)与裂解装置联产,副产氢气用于加氢工艺,形成丙烯-聚丙烯-高端新材料产业链。卫星化学通过整合PDH与乙烯装置,吨乙烯成本降低200美元。
未来趋势:技术迭代与产业协同
- ??原料多元化??:拓展丙烷来源,如页岩气伴生丙烷进口、生物丙烷制备,降低对外依存度。
- ??低碳化转型??:开发电加热裂解炉和CO2捕集技术,使碳排放强度下降40%。
- ??智能化控制??:应用AI模型预测结焦周期,实现清焦作业自动化,延长运行周期至60天以上。
通过上述技术创新与模式优化,丙烷裂解制乙烯技术正从单一烯烃生产向高附加值、低碳化的综合化工平台演进,为全球乙烯工业的可持续发展提供新范式。