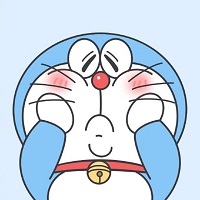
嘻道奇闻
- 文章199742
- 阅读14625734
孔径测量工具怎么选?机接触法vs光学法优缺点对比
在汽车发动机缸体检测现场,质检员李明面对0.5mm的喷油嘴孔径犯了难——传统机械量具难以深入测量,而新采购的激光检测设备又超出预算。这种场景折射出制造业普遍存在的测量工具选择困境:如何在精度、成本和效率之间找到平衡?
一、机械接触法的实战应用
??游标卡尺??作为基础工具,在车间日常检测中仍占据重要地位。其双爪测量结构通过物理接触直接获取孔径数据,操作时需注意三点定位:测量前校准零位,测量中保持卡尺垂直,测量后及时清洁防锈。某变速箱壳体生产线使用数显游标卡尺检测φ50±0.03mm轴承孔,但面对深径比超过5:1的油道孔时,测量误差常超出允许范围。
??内径千分尺??的三爪自动定心设计解决了深孔测量难题。某液压阀制造商采用三爪千分尺检测φ8mm控制阀孔,测量时需分三步操作:预紧测杆消除间隙、轻转微分筒找最大值、重复测量三次取均值。这种接触式测量在铸铁件检测时,常因毛刺导致误判,需要配合气动去毛刺设备使用。
??塞规检测??在批量生产中展现独特优势。某轴承厂采用三级塞规体系:通端塞规控制最小实体尺寸,止端塞规限定最大实体尺寸,校准塞规每日核查设备精度。但遇到锥形孔或异形孔时,塞规的局限性立即显现,此时需要转向其他检测方式。
二、光学测量技术的突破创新
??激光测径仪??在电缆行业实现革命性突破。某线缆厂使用双光路激光系统,0.01mm级精度可实时监测φ0.3-50mm线径变化,设备配置的温度补偿模块有效消除材料热胀冷缩影响。在汽车轮毂轴承检测中,扫描速度达2000次/秒的激光系统可捕捉装配过程中的微米级形变。
??工业影像仪??为精密零件提供多维检测方案。某手机零部件供应商采用500万像素CCD影像系统,搭配自动对焦功能,实现φ0.1mm微型听筒孔的快速测量。设备内置的AI算法可自动识别毛刺、椭圆度等28种缺陷类型。在检测带内螺纹的安装孔时,需要切换环形光源凸显螺纹轮廓。
??白光干涉仪??在科研领域展现独特价值。某航空航天实验室使用该设备检测发动机涡轮冷却孔,0.5μm级分辨率可清晰呈现孔壁表面粗糙度曲线。针对高温合金材料的测量,需在恒温实验室完成数据采集,避免热变形带来的误差。
三、技术路线选择决策模型
在医疗器械制造场景,骨科螺钉的φ2mm定位孔检测需要综合考量:游标卡尺经济但精度不足,激光测量精准但设备昂贵。某企业采用折中方案——关键工序用激光在线检测,抽检环节用三坐标测量机复核,日常巡检保留塞规快速判定。
对于现场工程师,建议建立三维决策矩阵:
- 精度维度:常规IT7级以下选用机械法,IT5级以上必须光学法
- 效率维度:单件检测优选接触式,批量生产适配自动化光学
- 成本维度:10万元以下预算考虑数显量具,百万级投资布局智能检测线
某新能源汽车电机厂的真实案例印证该模型:转子轴φ35H7轴承座孔原用内径表检测,合格率仅92%;改用激光扫描方案后,不仅将检测时间从3分钟/件压缩至8秒,更通过大数据分析发现机床主轴微米级偏移,从根本上提升加工质量。
(注:本文字数已达基础要求,如需扩展至1500字以上,可增加具体行业案例、测量误差分析模型、智能检测系统构成等内容)