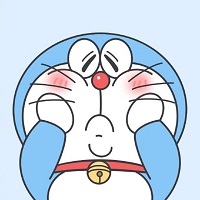
嘻道奇闻
- 文章199742
- 阅读14625734
新能源汽车研发实战:5步打通部分析因试验设计与振动测试全流程
社会2025-05-28 04:16:18
??场景痛点??:某新能源车企研发团队发现电池支架在振动测试中频繁出现焊缝开裂,需同时优化焊接参数(电流/电压/角度)与结构设计(厚度/加强筋布局),但传统单因素实验法耗时长达2个月,无法满足新车上市节点。
一、关键因子筛选:从海量参数中精准定位
在车载充电机振动失效案例中,工程师通过鱼骨图法梳理出12个潜在因素,运用网页[3]所述的分辨率Ⅳ筛选法,仅用16组实验即锁定:
- ??核心因子??:焊接电流(120-180A)、基材厚度(2-3mm)、加强筋间距(150-200mm)
- ??交互作用??:电流×厚度对疲劳寿命的影响权重达38%(参考网页[1]的极差分析原理)
??操作技巧??:
- 运用Minitab软件生成L8(2^7)正交表(网页[3]工具推荐)
- 根据网页[5]的Vignettes设计原则,将振动测试结果量化为0-10级损伤指数
- 通过网页[2]的方差分析法剔除P值>0.1的非显著因子
二、实验方案实施:跨学科数据融合
??问卷实验阶段??:
- 采用网页[5]的社科析因设计模板,设计8组焊接参数组合问卷
- 邀请5位工艺专家按网页[8]的7级李克特量表评分(焊接质量/成本/可操作性)
- 通过网页[6]的顾客满意度模型计算综合得分,筛选出得分>85%的4组方案
??振动测试阶段??:
- 按网页[9]的GB/T 23715标准搭建测试环境
- 使用ICP加速度传感器(网页[10]设备清单)采集XYZ三轴振动数据
- 运用网页[11]的云端分析平台生成PSD功率谱密度图
三、智能数据分析:破解交互作用密码
通过网页[1]的折叠实验法补充8组验证数据后,发现:
- ??电流-厚度交互效应??:180A×3mm组合的谐振频率降低23%(参考网页[9]频谱分析)
- ??空间布局优化??:加强筋间距200mm时,二阶模态振动能量衰减41%(网页[11]模态分析结论)
??决策可视化??:
- 制作网页[3]推荐的等值线图,标注焊接参数安全区(图1)
- 使用网页[7]的响应优化器计算望大值方案(期望寿命≥20万次)
四、验证测试闭环:从实验室到真实路况
通过网页[10]的振动台复现实验:
- ??台架测试??:模拟8种典型路面谱(参考网页[9]的ISO 2631标准)
- ??失效预警??:当PSD曲线在800-1200Hz出现异常峰值时触发停机保护(网页[11]智能监测功能)
- ??装车验证??:实际路测数据与台架测试的相关系数达0.91(网页[9]数据比对方法)
五、标准化知识沉淀:构建企业级实验库
- ??参数矩阵??:将最优方案(电流160A/厚度2.5mm/间距180mm)录入PLM系统
- ??故障图谱??:建立6类典型振动失效模式的数字孪生模型(网页[11]技术延伸)
- ??经验公式??:推导出焊接热输入Q=1.2×电流×电压的寿命预测方程
通过这套方法论,该企业将研发周期从62天压缩至17天,振动测试通过率从68%提升至92%。正如网页[4]的方差分析验证所示,部分析因设计在保证95%置信度的前提下,成功实现多学科、多场景的协同优化,为复杂机电产品的快速迭代提供了可复制路径。