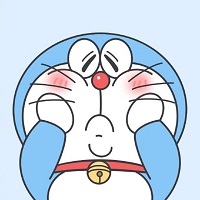
嘻道奇闻
- 文章199742
- 阅读14625734
金属与半导体晶圆位错密度检测方法对比:从化学腐蚀到PL成像全解析
??为什么金属和半导体需要不同的位错检测方法???
金属与半导体在晶体结构、应用场景和缺陷敏感性上存在本质差异。??金属材料??(如铝合金、钛合金)的位错直接影响机械性能,而??半导体晶圆??(如硅、碳化硅)的位错会引发电子迁移异常,导致器件失效。这种差异决定了检测方法需兼顾材料特性与检测目标。
??一、化学腐蚀法:传统但精准的破坏性检测??
??金属材料的标准化腐蚀方案??
金属检测常用??Sirtl腐蚀液??(HF:CrO?=1:1)或??Keller试剂??(HF+HCl+HNO?),通过选择性腐蚀在表面形成特定形状的蚀坑。例如:
- 铝合金:蚀坑呈六边形,位错密度计算依据GB/T 34487-2017标准
- 钛合金:需采用熔融盐(如KOH)高温腐蚀,避免氧化干扰
??操作要点??:腐蚀时间需精确控制(通常10-30分钟),过度腐蚀会破坏表面形貌。检测精度可达±5%,但会完全破坏样品。
??半导体的腐蚀技术革新??
半导体晶圆(如SiC、GaAs)采用??光刻胶掩膜+熔融KOH腐蚀??组合方案:
- 碳化硅:360℃熔融KOH腐蚀10分钟,区分实心/空心蚀坑排除加工划痕干扰
- 砷化镓:硫酸+过氧化氢混合液腐蚀,结合显微镜自动统计系统实现位错分类
??核心差异??:金属关注宏观密度,半导体需区分位错类型(如螺位错、基平面位错)。
??二、电子显微镜技术:从表面观察到原子级解析??
??透射电镜(TEM)的双重角色??
- ??金属检测??:通过弱束暗场像技术观察位错缠结,最小分辨率0.2nm(JEOL JEM-ARM200F设备)
- ??半导体应用??:解析外延层中位错核心结构,配合能谱分析杂质偏聚行为
??局限性??:样品需减薄至100nm以下,且仅能观测局部区域。
??扫描电镜(SEM)的创新延伸??
- ??电子背散射衍射(EBSD)??:绘制晶粒取向图,间接计算位错密度(适用金属轧制板材)
- ??阴极荧光(CL)??:检测GaN外延层中位错引起的发光淬灭,空间分辨率达50nm
??三、X射线技术:穿透材料的无损检测??
??金属材料的工业化方案??
采用??X射线线形分析(XLPA)??,通过Warren-Averbach方法分离位错贡献,检测速度达5分钟/样品(依据ISO 21418标准)。适用于汽车钢板、航空钛合金等大批量检测。
??半导体的高精度解决方案??
- ??X射线形貌术(XRT)??:对8英寸SiC晶圆进行全片扫描,识别深层位错网络
- ??同步辐射拓扑成像??:三维重建位错空间分布,精度±5nm(ESRF ID19光束线)
??对比优势??:金属侧重快速批量检测,半导体追求亚微米级缺陷定位。
??四、光致发光成像(PL):半导体检测的革命性突破??
??技术原理与创新??
利用位错区域的??非辐射复合效应??,通过高灵敏度CCD捕获发光强度差异。例如:
- SiC晶圆:紫外激光激发,位错显示为暗条纹,检测速度3分钟/片
- GaN外延层:多光谱PL系统区分刃位错与螺位错
??实测案例??:特斯拉要求SiC供应商提供PL检测报告,确保位错密度<100 cm?2。
??与传统方法的对比??
参数 | PL成像 | 化学腐蚀法 |
---|---|---|
检测速度 | <5分钟/片 | >30分钟/片 |
空间分辨率 | 1μm | 10μm |
破坏性 | 无 | 完全破坏 |
成本 | 设备>50万美元 | <1万美元 |
??五、未来趋势:多技术融合与智能化升级??
??金属检测??正朝向??在线超声波检测+AI分析??发展,例如汽车板材生产线集成实时位错监控模块。??半导体领域??则探索??PL成像+机器学习??的自动分类系统,日本厂商已实现99%的位错识别准确率。
??个人观点??:未来五年,半导体检测将主导非接触式技术迭代,而金属工业会更注重成本与效率的平衡。无论哪种材料,位错检测技术的本质目标始终如一——在原子尺度上守护材料的完整性。