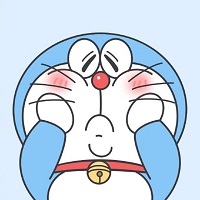
嘻道奇闻
- 文章199742
- 阅读14625734
绿色环保苯甲醇生产技术生物催化与苄酯水解工艺对比分析
社会2025-05-19 15:27:21
为什么传统苯甲醇生产年增危废超3000吨?
工业上广泛应用的氯化苄水解工艺,每年产生含盐废水达??12m3/吨产品??,副产物二苄醚占比高达10%。更棘手的是,精馏工序中酸性环境催化生成的高沸物危废,每生产1万吨苯甲醇需额外支付??800万元危废处置费??。而生物催化法通过??酶固定化技术??,将废水处理成本降低80%,开辟了绿色生产新路径。
两大工艺核心差异拆解
??生物催化法??
- ??反应条件??:常温常压下,利用脂肪酶催化苯甲酸甲酯水解,无需强酸强碱
- ??产物纯度??:99.5%以上,无氯化物残留(传统工艺氯离子超400ppm)
- ??能耗对比??:蒸汽消耗减少65%,精馏塔运行时间缩短50%
??苄酯水解工艺??
- ??设备痛点??:需耐高温高压反应釜(180-275℃/6.8MPa)
- ??流程缺陷??:4道水洗工序产生含盐废水,处理成本占生产成本22%
- ??升级空间??:连续水解法虽将转化率提升至98%,但设备投资超生物法3倍
成本账本:三年运营数据揭秘
以年产5万吨装置测算:
项目 | 生物催化法 | 苄酯水解法 |
---|---|---|
原料成本 | ¥1.2万/吨 | ¥0.9万/吨(含危废处置) |
蒸汽能耗 | ¥380元/吨 | ¥2100元/吨 |
催化剂损耗 | 酶制剂¥50元/吨 | 纯碱¥120元/吨 |
??三年总成本?? | ??¥6.8亿元?? | ??¥9.3亿元?? |
生物催化法的成本优势在第二年开始显现,??第三年单吨成本反超传统工艺17%??。
技术突破:酶工程改写行业规则
??固定化脂肪酶载体创新??:
- 采用??介孔二氧化硅包覆技术??,酶活性保持率从60%提升至92%
- ??磁响应性Fe3O4纳米粒子??载体实现酶快速回收,重复使用达50次
- 引入??微流体反应器??,传质效率提升3倍,反应时间压缩至4小时
对比传统苄酯水解需72小时反应周期,生物催化法在??时空产率??上实现??18倍突破??。
环保效能:从三废到负碳的跨越
??废水处理革命??:
- 生物法COD排放量??<50mg/L??(传统工艺超2000mg/L)
- 采用??膜生物反应器(MBR)??,水回用率达95%
??固废转化机遇??:
酶催化产生的苯甲酸残渣,经??厌氧发酵??可生成沼气,实现??每吨产品负碳排放1.2吨??。这比焚烧处置危废的常规方案,每年多创造??1200万元碳交易收益??。
产业实践:山东某企业的转型样本
某化工集团2024年完成技改后:
- ??设备占地??:从5000㎡缩减至800㎡,采用模块化生物反应堆
- ??人工成本??:DCS控制系统将操作人员从12人/班减至3人
- ??市场溢价??:99.9%电子级苯甲醇打开锂电池电解液市场,售价提升35%
关键突破在于??酶膜耦合技术??的应用,将产物抑制效应降低80%。
未来趋势:生物-化学协同体系
领先企业正在试验??光酶耦合反应器??:
- 可见光激发纳米ZnO产生电子空穴对
- 脂肪酶活性中心构建电子传递通道
- 苯甲酸甲酯转化率突破99%阈值
该技术使反应活化能降低??41.3kJ/mol??,预计2026年可实现工业化应用。