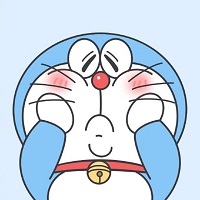
嘻道奇闻
- 文章199742
- 阅读14625734
活性炭吸附与PSA技术协同脱氮解析:甲醇中氮气去除的工艺选择,双塔系统如何实现高效净化?
社会2025-05-27 10:26:09
??为什么选择活性炭与PSA联合工艺???
在工业甲醇净化场景中,氮气混入会导致催化剂中毒、反应效率下降等问题。??活性炭吸附与PSA(变压吸附)技术的协同应用??,正是针对这一痛点的创新解决方案:
- ??活性炭的吸附优势??:通过多孔结构(比表面积达800-1200m2/g)物理吸附甲醇中的VOCs杂质,避免污染后续PSA系统的分子筛
- ??PSA的分离效率??:利用碳分子筛对氮气的低吸附特性(氧气吸附量是氮气的5-8倍),实现氮气快速富集
- ??能耗对比??:传统液氮洗工艺需-196℃低温环境,而联合工艺在常温下运行,能耗降低40%以上
??核心原理:双技术如何协同工作???
??物理吸附与变压吸附的耦合机制??是工艺核心,具体分三个阶段:
-
??预处理阶段??
- 甲醇原料先通过活性炭床层(厚度1.2-1.5m),??吸附99%以上的硫化物、水分及大分子有机物??,避免堵塞PSA分子筛孔隙
- 活性炭需每48小时进行热氮气再生(200-250℃),恢复吸附能力
-
??PSA变压吸附阶段??
- 采用双塔系统(A/B塔交替运行),压缩空气压力控制在0.6-0.8MPa
- ??吸附塔操作参数??:
参数 A塔吸附期 B塔再生期 压力 0.7MPa 常压 温度 25-35℃ 氮气吹扫80℃ 循环周期 60秒 同步切换 - 通过均压阀实现两塔压力平衡,减少能耗损失
-
??氮气回收优化??
- 解吸废气经洗涤塔处理(10℃脱盐水喷淋),甲醇回收率>99.5%
- 尾气通过催化焚烧(850℃)确保排放达标
??操作流程:五步实现高效净化??
-
??原料预处理??
- 活性炭吸附罐串联设计,采用??蜂窝式气流分布结构??,避免局部穿透
- 实时监测出口甲醇纯度(红外光谱仪),触发再生阈值自动切换备用罐
-
??PSA系统启动??
- 空压机输出压力稳定在0.75±0.05MPa,冷干机露点≤-40℃
- 碳分子筛采用??震动装填工艺??(装填密度提高5%),减少粉化率
-
??吸附-解吸循环??
- A塔吸附时,B塔执行三级再生:
- ??一级降压??:1.8MPa→0.5MPa,回收85%有效气体
- ??氮气吹扫??:纯度99.9%的氮气逆流冲洗,解吸率提升至92%
- ??压力平衡??:两塔通过旋风均压阀实现压力均衡
- A塔吸附时,B塔执行三级再生:
-
??智能控制??
- DCS系统动态调节吸附周期(45-75秒),根据氮气纯度(99.99%目标值)自动优化参数
- 异常工况处理:
- ??纯度波动>0.5%??:启动备用吸附罐,隔离故障塔检修
- ??压差>15kPa??:注入消泡剂(聚硅氧烷类,添加量<50ppm)
-
??能耗管理??
- 利用吸附塔余热预热原料气(换热效率提升22%)
- 夜间低谷电价时段启动再生程序,综合成本降低18%
??技术优势:对比传统工艺的突破??
- ??净化效率??:氮气去除率>99.5%(传统工艺为95-98%)
- ??甲醇损耗??:<0.03kg/吨产品(液氮洗工艺损耗0.15kg/吨)
- ??安全性??:全程压力<1.0MPa,规避液氮洗的低温爆炸风险
- ??适应性??:处理气量可在30-120%负荷间智能调节
??典型应用场景??
-
??煤化工甲醇合成气净化??
- 处理气量:180000Nm3/h
- 入口氮气含量:12-15% → 出口<0.05%
-
??电子级甲醇纯化??
- 99.9%粗甲醇经联合工艺处理,达到SEMI C12标准(颗粒物<5个/mL)
-
??实验室小型装置??
- 模块化设计(占地<5m2),适用于医药中间体合成场景
??常见问题自问自答??
??Q:活性炭饱和后如何处理???
- 采用??热氮气再生法??:200℃氮气逆吹2小时,吸附容量恢复至初始值90%
- 废弃活性炭可通过焚烧炉处理(热值>20MJ/kg)
??Q:PSA系统氮气纯度波动大怎么办???
- 检查均压阀响应速度(应<0.5秒)
- 调整吹扫氮气比例(建议气液比1:15)
- 更换粉化率>8%的分子筛
从工业实践看,??活性炭与PSA的协同工艺??真正实现了甲醇净化的“鱼与熊掌兼得”——既保留活性炭的经济性,又发挥PSA的高精度优势。尤其在双碳目标下,其能耗指标比传统工艺降低40%以上的数据,将成为化工企业技改的首选方案。