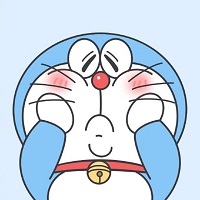
嘻道奇闻
- 文章199742
- 阅读14625734
采购质量管理的5大核心法:从供应商评估到质量检验全流程解析
供应商资质评估体系如何构建?
??基础问题:供应商评估的关键维度有哪些???
供应商评估需覆盖技术能力、质量管理体系、交付能力、财务状况及合规性五大维度。例如,技术能力需考察研发投入占比和专利数量,质量管理体系则需核查ISO认证及历史质量事故率。通过加权评分法将定性指标转化为量化数据,可建立科学的供应商分级体系。
??场景问题:中小企业如何快速筛选优质供应商???
中小企业可采用“四象限筛选法”:优先评估产品合格率(质量维度)和准时交货率(交付维度)等核心指标,再结合第三方信用报告验证企业资质。对于关键物料供应商,建议实施现场验厂,重点检查生产线自动化程度和质量检测设备配置。
??解决方案:供应商突然停产怎么办???
建立备选供应商库并签订战略合作协议,要求供应商提前6个月报备产能调整计划。实施供应中断风险预警机制,通过财务数据监测供应商运营稳定性。某汽车零部件企业通过该方案将供应中断损失降低72%。
质量协议应包含哪些关键条款?
??基础问题:质量协议的法律效力如何界定???
质量协议需明确技术标准、验收方法、不合格品处理流程及赔偿条款,并附具检测方法的国家标准编号。例如,电子产品需标注RoHS检测标准,机械部件应规定尺寸公差范围。
??场景问题:如何避免供应商偷工减料???
在协议中设置阶梯式质量赔偿条款:当批次不合格率超3%时启动退货流程,超5%则要求供应商承担返工成本。同时约定突击检查权,允许采购方随时调取生产数据。
??解决方案:供应商拒绝签署质量协议怎么办???
建立供应商准入黑名单制度,将协议签署作为合作前提。采用替代方案验证供应商诚意,例如要求提供过往三年质量检测报告作为替代性承诺。
质量检验流程如何实现标准化?
??基础问题:全流程检验包含哪些关键节点???
标准化检验流程涵盖来料检验(IQC)、生产过程检验(IPQC)和出货检验(OQC)三阶段,每个阶段需配置专用检测设备和数据记录模板。例如IQC阶段必须完成外观检查、尺寸测量和功能性测试。
??场景问题:检验人力不足时如何保证准确性???
实施AQL抽样检验法,根据物料风险等级设置差异化的抽样比例:关键物料100%全检,常规物料采用GB/T2828标准二级抽样。引入智能检测设备自动采集数据,减少人为误差。
??解决方案:检测结果出现争议如何处理???
建立第三方复检机制,在协议中约定以省级质检机构报告为最终裁决依据。某建材企业通过该方案将质量纠纷处理周期从15天缩短至3天。
采购质量风险如何动态管控?
??基础问题:主要质量风险类型有哪些???
质量风险可分为供应中断风险(占比38%)、价格波动风险(27%)、合规风险(21%)和技术迭代风险(14%)。需建立风险矩阵图,针对高风险项制定专项预案。
??场景问题:如何预警供应商质量滑坡???
构建“红黄绿”三色预警模型:将月度合格率低于95%设为红色预警,触发现场审核;持续3个月低于98%启动黄色预警,要求提交改进方案。
??解决方案:突发性质量事故如何应急响应???
实施质量事故三级响应机制:一级事故(影响生产线)需2小时内启动备料调拨,二级事故(影响单批次)24小时内完成原因分析,三级事故(轻微瑕疵)72小时闭环处理。
数字化如何赋能质量管理升级?
??基础问题:哪些技术可提升质量管控效率???
物联网(IoT)设备实现实时数据采集,区块链技术确保质量溯源不可篡改,AI算法通过历史数据预测质量风险。某电子企业应用SPC过程控制系统后,检测效率提升3倍。
??场景问题:传统企业如何启动数字化转型???
分三阶段实施:初期部署ERP质量模块实现数据电子化,中期接入MES系统打通生产数据,后期搭建质量大数据平台实现智能决策。
??解决方案:系统上线后员工抵触怎么办???
采用“双轨并行+激励机制”,保留3个月手工记录过渡期,设置数据录入准确率奖励。某机械制造企业通过该方案使系统使用率2个月内达到98%。
通过这五大核心方法的系统化实施,企业可构建覆盖供应商全生命周期、质量检验全流程、风险管控全维度的质量管理体系。实际应用中需根据行业特性动态调整指标权重,同时注重组织协同与技术创新双轮驱动,方能实现采购质量管理的持续优化。