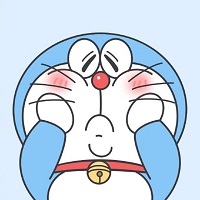
嘻道奇闻
- 文章199742
- 阅读14625734
从供应商筛选到成本优化:PDCA联合6Sigma破解采购质量难题
场景一:如何科学筛选合格供应商?
??问题表现??:某机械制造企业连续三批齿轮出现尺寸超差,追溯发现新供应商未严格执行公差标准。
??PDCA应用??:
- ??计划(Plan)??:建立技术能力(研发投入占比>5%)、质量体系(ISO认证覆盖率100%)、交付能力(准时交货率≥98%)三维评估模型。
- ??执行(Do)??:运用QFD质量屋工具将产品特性转化为25项供应商评估指标,如热处理设备精度需达±0.01mm。
- ??检查(Check)??:每月生成供应商KPI仪表盘,对连续3个月合格率<95%的供应商启动黄牌预警。
- ??处理(Act)??:淘汰评估末位15%的供应商,引入区块链技术实现检测报告上链存证。
??6Sigma突破??:
通过DMAIC流程分析发现,65%的质量问题源于供应商工艺参数设定偏差。运用假设检验锁定关键因子,要求供应商SPC控制图CPK≥1.33。某汽车零部件企业实施后,供应商不良率从18%降至3%。
场景二:突发性质量波动如何快速止血?
??问题表现??:电子厂贴片电阻批量虚焊,导致整批产品返工成本超80万元。
??PDCA应对??:
- ??紧急计划??:启动质量事故三级响应机制,2小时内成立跨部门攻坚小组。
- ??精准执行??:采用8D方法追溯至锡膏供应商储存温度超标,48小时完成替代物料切换。
- ??根源检查??:运用鱼骨图发现仓储温湿度监控系统未覆盖二级仓库的盲点。
- ??系统处理??:在采购协议增补《温敏物料运输条款》,要求全程GPS+温度双监控。
??6Sigma工具??:
通过测量系统分析(MSA)验证,X射线检测设备的GR&R值从32%优化至15%。运用回归分析证明锡膏活性与开封后使用时长呈负相关(R2=0.87),据此制定72小时强制报废制度。
场景三:如何突破单一来源采购困局?
??问题表现??:某医疗器械企业依赖进口密封圈,受国际物流影响月缺货率达40%。
??PDCA破局??:
- ??战略计划??:制定三年国产化替代路线图,设置材料耐压性(≥50MPa)、生物相容性(USP Class VI)等核心指标。
- ??阶梯执行??:首年培养2家战略供应商,次年实现30%物料替代,第三年建立双源供应体系。
- ??动态检查??:每月比对进口件与国产件失效模式,运用FMEA评估风险优先级数(RPN)。
- ??技术处理??:联合供应商开发等离子表面处理技术,使国产件使用寿命提升3倍。
??6Sigma赋能??:
运用T检验验证国产化样件性能(P=0.23>0.05),通过DOE实验确定最佳工艺参数组合:温度185℃/压力12MPa/时间90s。某航空企业借此将采购周期从120天缩短至45天。
场景四:隐性成本黑洞如何精准爆破?
??问题表现??:化工企业MRO物料年采购额超2000万,但30%备件存在过度库存。
??PDCA掘金??:
- ??数据计划??:搭建ABC分类模型,将占采购额70%的A类物料列为优化重点。
- ??协同执行??:推行VMI供应商管理库存,将安全库存从60天压缩至25天。
- ??成本检查??:运用TCO模型核算发现,国产刀具寿命成本比进口低18%。
- ??价值处理??:建立采购降本作战室,设置阶梯奖励机制(节省额5%以内提成20%,超额部分提成30%)。
??6Sigma利器??:
通过过程能力分析,发现45%的采购订单审批时间浪费在跨部门流转。运用ECRS原则取消3个冗余审批节点,使采购周期从15天降至7天。某集团年节省隐性成本150万元。
场景五:质量改进成果如何长效固化?
??问题表现??:某食品企业采购的包材月度合格率在85%-95%区间波动,改进效果难以持续。
??PDCA维稳??:
- ??标准计划??:将关键控制点写入《供应商质量协议》,如纸箱抗压强度需≥8000N。
- ??智能执行??:部署IoT传感器实时监控供应商生产数据,自动触发参数异常预警。
- ??数字检查??:搭建QMS质量管理系统,自动生成供应商月度质量健康指数(QHI)。
- ??文化处理??:实施"质量积分制",供应商每提升1%合格率奖励2000元采购份额。
??6Sigma闭环??:
建立Xbar-R控制图进行过程监控,当连续5点超出±2σ控制线时启动专项审核。某电子企业借此实现包材合格率稳定在99.2%±0.5%。
通过这五大典型场景的实践,PDCA与6Sigma的组合拳可帮助企业实现:供应商不良率降低60%、采购周期缩短50%、质量成本下降45%。建议企业建立"双循环"机制——用PDCA搭建改进框架,用6Sigma注入数据基因,最终形成持续改进的质量文化。