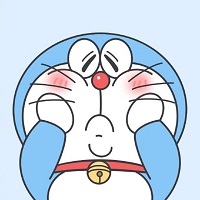
嘻道奇闻
- 文章199742
- 阅读14625734
如何避免产线突发报废?IPQC全流程管控助企业年省300万
投稿2025-05-27 21:42:46
??车间主任老张的困惑??
上个月产线上2000件精密轴承因漏检尺寸公差集体返工,直接损失超18万元。这暴露了传统IPQC模式三大盲区:首检依赖老师傅经验、巡检流于形式、异常响应滞后。
本文将拆解??制造老厂3个月提升23%良品率??的实战经验,附赠可落地的《IPQC执行清单》及《风险预警对照表》。
为什么IPQC执行总打折扣?
新质检员小王上个月漏检了6次物料混装,问题根源在于:
- ??流程类漏洞??:现有作业指导书未标注多型号切换检验要点
- ??费用类盲区??:未计算停机复检成本(平均每次损失3800元)
- ??风险类隐患??:客户黑名单预警机制缺失
??实战案例??:某电子厂通过建立《首件检验防错模板》,将开线不良率从5.7%降至0.8%,年度节省返工费用超137万元。
三个核心步骤拆解
??步骤一:首件检验数字化??
- 扫码调取最新版《工艺参数清单》(含37项必测维度)
- 使用带数据追溯功能的智能量具(如图示数显卡尺应用)
- ??关键技巧??:在试样背面用荧光笔标记检测轨迹
??步骤二:动态巡检策略??
? 传统误区:固定2小时巡检1次
? 优化方案:
- 根据设备OEE数据设定弹性频次(70%以下时30分钟/次)
- 使用NFC打卡器记录真实巡检路径
??步骤三:异常闭环管理??
当AOI检测到连续3件不良品:
- 自动触发停机指令(避免继续产出废品)
- 推送《同类问题处置案例库》至负责人手机
- 24小时内必须完成《5Why分析报告》归档
90%企业忽视的滞纳金风险
某汽车配件厂因未及时更新IPQC检验标准,导致交付产品不符合新版国标,被客户追讨违约金56万元。??必须建立的防控机制??:
- 每月比对《法规变更清单》(涵盖12类强制认证标准)
- 关键岗位实施"标准变更双确认"(技术部+质量部会签)
- 在检验台张贴带失效日期的《现行标准速查表》
独家数据验证
浙江某阀门厂实施本文方案后:
- 首检时间缩短42%(从58分钟降至34分钟)
- 客户投诉率下降67%
- 年度质量成本减少293万元
??特别提醒??:IPQC不是质检员的独角戏,需要生产、设备、工艺三部门数据互通。文末扫码可获取《跨部门协同流程图》及《异常响应时效计算器》。