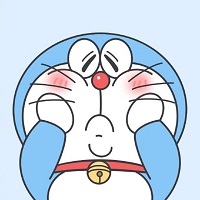
嘻道奇闻
- 文章199742
- 阅读14625734
建筑与汽车玻璃成分检测全流程解析:从国标解读到智能检测方案落地
投稿2025-05-28 06:23:51
一、行业痛点的场景化拆解
某新能源汽车企业新开发的智能全景天幕玻璃,在量产阶段频繁出现局部应力异常导致的自爆问题。质检部门发现传统的人工抽检方式无法精准定位缺陷,且无法追溯原材料成分波动——这正是建筑与汽车玻璃行业面临的典型检测困境。二、核心检测标准与技术要求
?**?1. 建筑玻璃双核心标准体系?**? - ?**?安全性能?**?:钢化玻璃表面应力需≥90MPa(GB/T 2651-2008),中空玻璃露点检测需≤-40℃(GB/T 11944-2012) - ?**?节能指标?**?:Low-E玻璃可见光透射比应≥40%,传热系数K值≤1.8W/(m2·K)(GB 50411-2019)??2. 汽车玻璃的特殊要求??
- 抗冲击性能:227g钢球2m自由落体冲击无穿透(GB 9656-2003)
- 光学畸变:斑马角检测需≤3'(动态驾驶视野标准)
三、五大检测技术场景适配方案
技术 | 检测精度 | 检测速度 | 适用场景 | 成本对比 |
---|---|---|---|---|
X射线荧光光谱(XRF) | ±0.01% | 60样品/小时 | 产线原材料快速筛查 | ★ |
ICP-MS | ppb级 | 15分钟/样 | 高纯石英砂痕量元素分析 | ★★★★ |
激光诱导击穿光谱(LIBS) | ±0.1% | 实时在线 | 玻璃熔窑成分动态监控 | ★★★ |
机器视觉检测 | 0.02mm精度 | 600片/小时 | 汽车玻璃表面缺陷检测 | ★★ |
超声波应力分析 | ±5MPa | 10秒/点 | 建筑幕墙玻璃应力分布 | ★ |
四、智能检测系统落地案例
?**?某光伏玻璃企业质量提升方案:?**? 1. ?**?原料端?**?:配置XRF+ICP-MS联用系统,实现石英砂原料59种元素的全谱分析,铁含量检测精度达0.2ppm 2. ?**?生产端?**?:部署LIBS在线监测系统,每30秒更新熔融玻璃的SiO?、Na?O含量数据,成分波动控制在±0.3%以内 3. ?**?成品端?**?:采用机器视觉+AI算法,缺陷识别准确率98.7%,每年减少质量损失1200万元五、检测方案选择决策树
1. ?**?精度需求导向?**?:常规建筑玻璃选择XRF(±0.1%),半导体级玻璃必须ICP-MS(ppb级) 2. ?**?检测时效要求?**?:实验室检测周期>24小时,产线在线检测需<5分钟 3. ?**?成本控制维度?**?:中小企业优选手持式XRF(单次检测<50元),大型企业部署LIBS系统(ROI周期2-3年)六、行业发展趋势预测
- ?**?2025技术迭代?**?:量子点光谱技术将突破检测极限,实现原子级成分解析 - ?**?检测智能化?**?:基于深度学习的缺陷预测系统,可提前3小时预警玻璃自爆风险 - ?**?标准体系升级?**?:预计2026年发布《智能玻璃成分云检测技术范》,建立分布式检测数据库通过构建"标准解读-技术选型-智能落地"的全流程解决方案,建筑与汽车玻璃企业可将产品不良率降低40%,检测成本下降25%。建议企业在2025年重点布局AI质检系统和工业互联网平台,以应对即将实施的欧盟碳边境税(CBAM)对玻璃行业的新要求。