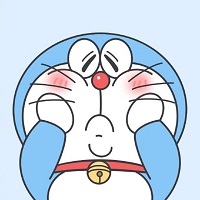
嘻道奇闻
- 文章199742
- 阅读14625734
三步精准定位高价值存货:ABC分类法实战指南
投稿2025-05-27 13:26:46
场景一:仓库爆仓但核心物料总缺货
??现象??:某电子产品仓库堆满螺丝、包装盒等低值品,价值百万的芯片却频繁缺货导致产线停工。
??核心矛盾??:管理精力分散,导致20%高价值物料供应不足与80%低价值物料积压并存。
??解决方案??:
- ??数据采集与价值排序??
提取近1年所有物料的采购金额、周转次数、缺货影响系数,按总价值降序排列。某汽车配件企业发现:仅占库存总数12%的发动机部件,贡献了78%的库存价值。 - ??动态分类调整机制??
设置季度重分类规则:当某物料连续3个月采购额超阈值,自动升为A类。某化工企业通过动态调整,使A类物料缺货率下降60%。 - ??分级存储策略??
将A类物料存放在距出货口5米内的智能货架区,B类置于中层阁楼货架,C类采用"双堆法"存放于仓库边缘。某电商仓实施后,拣货效率提升2.3倍。
场景二:采购资金被低效占用
??现象??:某服装企业每月80%采购预算用于纽扣、线材等低值品,导致当季爆款面料采购不足。
??解决方案??:
- ??差异化采购策略??
A类面料:与3家核心供应商签订VMI协议,按日补货
B类辅料:采用经济批量模型,计算最佳采购量Q=H2DS??
C类耗材:实行年度招标,一次性采购全年用量 - ??资金监控看板??
建立ABC类资金池仪表盘,当C类采购占比超15%时自动预警。某制造企业通过该机制释放38%流动资金。 - ??供应商分级管理??
对A类物料供应商实施"1+2"备份机制(1家主力+2家备选),某手机厂商借此将芯片供应稳定性提升至99.7%。
场景三:盘点耗时却数据失真
??现象??:某快消品仓库每月全盘耗时72小时,但A类饮料的库存误差仍达15%。
??解决方案??:
- ??智能盘点组合拳??
A类:RFID每日循环盘点 + UWB定位追踪
B类:PDA每周抽盘(比例≥30%)
C类:视觉识别季度盘点
某物流企业采用该模式后,盘点效率提升400%。 - ??异常处理流程??
建立分级响应机制:A类物料差异超2%立即溯源,C类差异超20%才触发调查。某医药仓借此将质量事故响应时间缩短至4小时。 - ??容错空间设置??
允许C类物料±15%库存偏差,重点监控A类物料±3%波动带。某精密仪器企业库存准确率从82%提升至98.6%。
持续优化四步法
- ??建立价值-风险矩阵??
将物料按采购金额(纵轴)和供应风险(横轴)四象限划分,对高价值高风险物料实施"双锁管理"(物理锁+数字权限)。 - ??异常场景沙盘推演??
每季度模拟A类物料断供、C类物料暴涨等10种场景,某半导体企业通过推演将危机应对时间缩短58%。 - ??数字化看板构建??
开发三色预警看板:A类红色预警联动生产计划,C类黄色预警仅需库管确认。 - ??人员能力匹配??
设置ABC类管理师认证体系,A类物料操作需三级认证资质。某汽车厂实施后,库存损耗下降72%。
通过这三个典型场景的解决方案,企业可构建"分类-执行-优化"的闭环管理体系。数据显示,科学应用ABC分类法可使库存周转率提升40-60%,仓储成本降低25-35%。随着物联网技术的深化应用,未来ABC分类将实现实时动态调整,真正达成"重要物料零缺货,冗余库存趋近零"的管理目标。