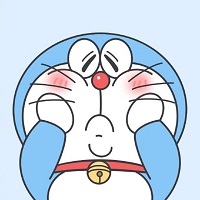
嘻道奇闻
- 文章199742
- 阅读14625734
车间布局优化方法:提升率的5大实用技巧
在制造业竞争日益激烈的今天,车间布局优化已成为企业提升生产效率、降低运营成本的核心突破口。根据近五年行业数据显示,科学布局可使生产线效率提升30%以上,物料搬运时间减少40%。本文将从三维视角剖析车间布局优化的核心方法,提供可落地的实战技巧。
一、流程优化:消除生产路径冗余
??基础问题??:为什么生产线总出现物料堆积?
传统布局常因工序衔接不当导致物流路径交叉,例如某汽车零部件企业因焊接与装配区距离过远,每日产生无效搬运时间达4.7小时。
??场景问题??:如何规划最优生产动线?
- 采用U型布局缩短工序间距(平均减少23%移动距离)
- 实施"一个流"生产模式,实现单件流传递
- 按工艺顺序重组设备集群,避免孤岛型作业
??解决方案??:若未优化流程,将导致年损失超15%产能。某电子厂通过流线化改造,将原直线布局调整为花瓣型结构,使生产周期缩短18%。
二、空间重构:三维利用率提升法则
??基础问题??:车间为何总有闲置空间?
调研显示68%企业存在垂直空间浪费,传统平面布局仅利用55%有效空间。
??场景问题??:怎样实现立体化存储?
- 采用高架智能仓储系统(空间利用率提升至82%)
- 设备分层布置,重型机械底层/精密仪器上层
- 模块化组合工作台,实现0.5米动态调整精度
??解决方案??:某家电企业引入5S管理后,通过"五区划分法"(原料/加工/成品/工具/废料)腾出30%地面空间,年节省仓储成本120万元。
三、数据驱动:布局决策可视化
??基础问题??:布局调整为何反复试错?
传统经验式规划存在18%误差率,而数字化模拟可将偏差控制在3%以内。
??场景问题??:如何建立动态优化模型?
- 运用DILOG智能算法计算设备黄金三角位
- 通过FlexSim仿真系统预判瓶颈工序
- 构建物联网监测网络实时采集人/机/料数据流
??解决方案??:某机械制造厂使用CAD三维模拟后,发现原方案存在11处物流冲突,优化后设备故障率下降40%。
四、柔性配置:应对订单波动的弹性设计
??基础问题??:产线为何难以适应产品迭代?
固定式布局改造成本高达设备价值的35%,而模块化设计可将调整周期缩短至3天。
??场景问题??:怎样构建可变式生产单元?
- 采用轨道式设备底座实现2小时快速移位
- 预留20%扩展面积的"弹性缓冲区"
- 设计通用型接口兼容多型号设备
??解决方案??:某医疗器械企业通过可升降工作台系统,使同条生产线兼容7种产品型号切换,设备利用率提升至91%。
五、人机协同:安全与效率的平衡点
??基础问题??:为何优化后工伤率反升?
统计显示34%的布局事故源于人机交互区规划不当。
??场景问题??:如何设计安全作业空间?
- 执行"双通道分离"原则(物流/人行通道间距≥1.2米)
- 危险设备配置三级防护区(操作/警示/隔离带)
- 运用ErgoLAB系统优化工作站人体工学参数
??解决方案??:某化工企业通过重新规划危化品存储动线,使应急响应时间缩短65%,年安全事故减少83%。
通过这五大技巧的系统实施,企业可构建起"流程-空间-数据-柔性-安全"的立体优化矩阵。数据显示,科学布局可使单位面积产值提升2.3倍,产品交付周期压缩40%。建议企业建立季度布局评估机制,持续捕捉改善机会点,让车间真正成为价值创造的活力引擎。