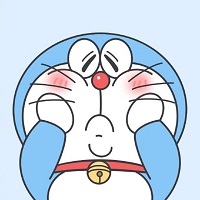
嘻道奇闻
- 文章199742
- 阅读14625734
机械加工必看:钻孔、铰、镗孔等8种孔加工方法全解析
钻孔:孔加工的基础步骤
??为什么钻孔被称为孔加工的第一道工序???
钻孔是唯一能在实体材料上直接开孔的工艺,常用麻花钻完成,精度一般为??IT13~IT11级??,表面粗糙度??Ra 50~12.5μm??。其核心优势在于效率高,但存在钻头易偏斜、排屑困难等问题。
??关键应用场景??:螺栓孔、油道孔、线切割穿丝孔等非精密需求场景。
??钻孔的两种加工方式对比??:
- ??钻头旋转??(如钻床加工):易导致孔轴线偏斜,但孔径稳定。
- ??工件旋转??(如车床加工):孔轴线笔直,但可能产生孔径误差。
扩孔与铰孔:从粗加工到精加工的升级
??扩孔如何提升孔的质量???
扩孔钻齿数多(3~8齿)、无横刃,可修正钻孔的轴线偏差,将精度提升至??IT11~IT10级??,表面粗糙度降至??Ra 12.5~6.3μm??。常用于直径小于30mm的孔半精加工。
??铰孔为何是精密孔的终选方案???
铰刀通过微量切削(余量0.05~0.35mm)实现??IT7~IT9级精度??和??Ra 0.8~3.2μm??表面质量。但需注意:铰孔无法修正孔位偏差,仅适用于通孔加工。
镗孔:大尺寸与高精度的平衡艺术
??镗孔如何解决大孔径加工难题???
镗刀可加工直径达1000mm的孔,精度达??IT6~IT7级??,尤其适合箱体类零件的孔系加工。其核心优势在于:
- ??单刃镗刀??:灵活调整孔径,适合单件小批量生产。
- ??双刃镗刀??:对称切削力抵消振动,精度稳定,适合批量加工。
??镗孔三大加工方式对比??:
- 工件旋转(车床):保证孔与外圆同轴度。
- 刀具旋转(镗床):适合复杂孔系加工。
- 刀具旋转+进给:仅用于短孔,易产生锥度误差。
珩磨与拉孔:高效精密加工的秘密
??珩磨为何是发动机缸体的终极工艺???
珩磨头通过旋转+往复运动,以磨削+擦拭方式实现??IT6~IT7级精度??和??Ra 0.2μm??镜面效果,尤其擅长修正深孔直线度。
??拉孔如何实现“一刀成型”???
拉刀一次走刀完成粗、精、光整加工,效率比传统方法高5倍以上,精度达??IT7~IT9级??,但刀具成本高,仅适合大批量生产。
深孔加工:枪钻与BTA钻的技术突破
??深孔(L/D>5)加工的核心挑战是什么???
排屑难、散热差、刀具易偏斜。解决方案:
- ??枪钻??:适用于L/D=5~20的孔,内冷设计强制排屑。
- ??BTA钻??:高压切削液从钻杆外部注入,适合L/D>20的特殊深孔。
其他孔加工方法:特种工艺的应用边界
- ??激光加工??:微孔(<0.1mm)首选,无刀具磨损,但成本高。
- ??电火花加工??:硬质合金孔加工,精度±0.01mm,速度慢。
- ??挤压加工??:无切屑成形,表面硬化提升疲劳强度,适合轴承孔。
如何选择最佳孔加工方法?
??精度、效率、成本的三角博弈??:
方法 | 精度等级 | 表面粗糙度(Ra/μm) | 适用场景 |
---|---|---|---|
钻孔 | IT11~13 | 12.5~50 | 非配合孔、预加工 |
铰孔 | IT7~9 | 0.8~3.2 | 精密配合孔(<φ50mm) |
金刚镗 | IT6~7 | 0.4~0.8 | 高精度有色金属孔 |
珩磨 | IT6~7 | 0.2~0.4 | 液压缸、发动机缸体 |
??个人观点??:在智能化制造趋势下,建议优先考虑复合加工方案——例如“钻+铰”组合刀具实现钻孔与精加工一站式完成,可比传统工艺减少30%的换刀时间。对于难加工材料(如钛合金),采用超声辅助钻孔或低温钻孔技术,能显著提升刀具寿命2倍以上。