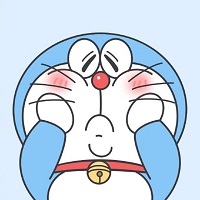
嘻道奇闻
- 文章199742
- 阅读14625734
车床锥度加工3大方法详:从操作步骤到角度校准
奇闻2025-05-28 08:31:22
为什么车削锥度总出现角度偏差?
在机械加工中,??锥度精度误差超过0.1°就会导致零件报废??,特别是配合精度要求高的锥面(如机床主轴孔与顶尖配合)。通过分析常见加工故障发现,??60%的锥度误差源于角度校准失误??。本文将详解3大核心加工方法及校准技巧,帮新手快速掌握锥度加工核心技能。
方法一:转动小滑板法(精度±0.5°)
??适用场景??:短锥面(长度<150mm)、单件或小批量生产
??操作步骤??:
- ??角度计算??:根据公式 tan(α/2)=(D-d)/(2L) ,α为圆锥角,D/d为大/小端直径,L为锥长。
- ??调整滑板??:松开小滑板锁紧螺母,按计算结果旋转刻度盘(如锥度1:10对应角度2°52')。
- ??试切校准??:先车削5mm长度,用万能角度尺检测实际角度,偏差超过0.5°时需重新调整。
??新手避坑??:
- ??刀具必须对准工件中心??,否则会产生双曲线误差
- 每次调整角度后需重新锁紧滑板螺母,避免加工震动导致偏移
方法二:偏移尾座法(精度±0.2°)
??适用场景??:长轴类锥面(长度>200mm)、批量生产
??核心公式??:
尾座偏移量 S = L0×(D-d)/(2L) ,其中L0为工件总长。
??操作流程??:
- ??安装双顶尖??:在主轴端和尾座顶尖间装夹工件
- ??计算偏移量??:例如加工1:20锥度、总长300mm的轴,偏移量S=300×1/20=15mm
- ??百分表校准??:将百分表固定在刀架上,移动大拖板检测尾座偏移量是否达标
??技术优势??:
- ??可自动走刀加工??,表面粗糙度Ra≤3.2μm
- 避免手动进给力度不均导致的锥面波纹
方法三:锥度附件法(精度±0.1°)
??设备要求??:需配备锥度靠模装置,适合数控车床或精密车床
??操作要点??:
- ??参数设置??:在数控系统中输入锥度角、起始/终止直径
- ??编程示例??:
markdown复制
G01 X40 Z0 F0.2 //起点直径40mm X20 Z-50 //终点直径20mm,锥长50mm
- ??在线检测??:利用机床探头实时测量锥度,自动补偿刀具磨损误差
??精度对比??:
方法 | 角度误差 | 表面粗糙度 | 适用场景 |
---|---|---|---|
小滑板法 | ±0.5° | Ra3.2 | 短锥、单件 |
偏移尾座法 | ±0.2° | Ra1.6 | 长轴、批量 |
数控附件法 | ±0.05° | Ra0.8 | 精密配合件、数控加工 |
角度校准4大实战技巧
-
??百分表校正法??:
- 将百分表吸在小滑板上,沿标准锥规移动50mm
- 表针摆动量应≤0.01mm,否则需微调角度
-
??涂色检测法??:
- 在锥面均匀涂抹红丹粉,与标准量规配合旋转1/4圈
- ??接触面>75%??为合格,小端接触需增大角度
-
??三角函数验证??:
- 测量大端直径D和小端直径d
- 实际锥角α=2×arctan[(D-d)/(2L)],与理论值偏差应<0.1°
-
??数控补偿策略??:
- 首件加工后测量实际锥角
- 在程序中加入刀补参数(如#5021=#5021+0.005)
加工参数优化指南
??切削三要素选择??:
- ??进给速度??:粗加工0.3-0.5mm/r,精加工0.1-0.2mm/r
- ??切削深度??:硬质合金刀具建议≤2mm,高速钢刀具≤1mm
- ??转速公式??:n=1000Vc/(πD),45钢取Vc=120-150m/min
??独家数据??:
某变速箱企业通过优化锥度加工工艺,将锥面配合不良率从12%降至0.8%,单件加工时间缩短22分钟。掌握这些核心方法,你也能实现高精度锥面加工!